Secret Advantages of Utilizing Plastic Shot Molding in Production
Plastic shot molding has actually arised as an essential method in the manufacturing industry, supplying an array of benefits that considerably enhance manufacturing processes. Notable benefits consist of amazing production effectiveness, the capability for detailed layouts, and a positive price framework that appeals to organizations of all dimensions.
High Manufacturing Performance
One of the most substantial benefits of plastic injection molding is its high production performance, which can result in the rapid production of thousands of similar parts within a brief timeframe. This effectiveness is largely credited to the automatic nature of the injection molding procedure. When the first configuration and mold and mildew development are finished, the manufacturing of parts can be scaled up considerably without a corresponding boost in labor expenses or time.
The process typically includes home heating plastic pellets until they thaw, injecting the molten material right into a precisely made mold, and allowing it to solidify and cool down - Plastic Injection Molding. This cycle can be finished in plain seconds to mins, depending upon the intricacy and dimension of the component being generated. Consequently, makers can attain high result rates, making plastic shot molding an optimal option for automation
Additionally, the capability to create huge amounts consistently makes certain lower device prices, making it a cost-effective remedy for services. This production effectiveness not only fulfills market needs quickly but likewise improves the overall competition of suppliers in numerous industries. Plastic shot molding remains a preferred technique for high-volume production applications.
Layout Flexibility
The capacities of plastic injection molding extend beyond high manufacturing efficiency to include significant layout adaptability. This production process enables designers and developers to develop detailed and complex forms that could be challenging or impossible to accomplish with various other methods (Plastic Injection Molding). The capability to quickly adapt and change mold layouts means that suppliers can promptly react to transforming market demands and innovate brand-new product designs without substantial retooling
In addition, plastic shot molding supports a vast array of materials, including various thermoplastics and thermosetting polymers. This selection makes it possible for the manufacturing of elements with special residential properties, such as boosted stamina, lightweight features, or certain thermal and electric attributes. In addition, the process enables the integration of numerous attributes into a single component, decreasing the requirement for setting up and reducing prospective factors of failure.
The precision of injection molding additionally makes sure that elements are generated with tight resistances, boosting fit and feature. The versatility to produce tiny to huge batches successfully even more underscores its versatility, making it a perfect choice for both prototyping and large production. On the whole, design versatility is a foundation advantage of plastic injection molding, driving development in numerous sectors.
Cost-Effectiveness
Cost-effectiveness sticks out as a considerable advantage of plastic shot molding in production. This procedure permits the automation of premium plastic components at a fairly reduced expense each, especially when compared to various other producing techniques. The efficiency of shot molding exists in its capability to generate complex forms with minimal waste, optimizing product use and reducing general expenses.
Furthermore, the rate of production is a vital consider cost-effectiveness. When the initial mold and mildew is created, the moment called for to generate each subsequent component is substantially reduced, leading to boosted output and faster turnaround times. This quick production capacity not only meets high-volume demands but additionally minimizes labor prices, as automated systems can deal with a lot of the process.
Additionally, the durability and durability of injection-molded products add to their cost-effectiveness over time. These components typically need much less maintenance and replacement, resulting in reduced lifecycle prices for end-users and makers alike. In recap, the cost-effectiveness of plastic shot molding makes it an appealing alternative for businesses seeking to enhance their manufacturing efficiency while preserving product high quality.
Product Flexibility
Material adaptability is a hallmark of plastic injection molding, allowing suppliers to select from a large variety of polymers that fulfill certain efficiency requirements. This flexibility permits for the production of elements customized to different applications, varying from vehicle components to consumer items.
Commonly made use of products include acrylonitrile butadiene styrene (ABDOMINAL MUSCLE), polycarbonate (PC), and polypropylene (PP), each offering distinct properties such as influence resistance, heat tolerance, and chemical security. Manufacturers can choose materials based on features like strength, weight, and thermal stability, making certain the end product meets practical and aesthetic needs.
Additionally, the capacity to integrate different polymers via co-injection techniques further boosts product versatility. This allows for the development of multi-layered components with distinct characteristics, such as soft-touch surfaces incorporated with rigid structural elements.
Additionally, improvements in recycled and naturally degradable products are expanding the choices available, straightening with sustainability goals in manufacturing. Generally, the diverse product choices in plastic injection molding empower suppliers to innovate and maximize their products, promoting the development of highly specialized and competitively useful remedies.
Boosted Product Longevity
Improved item resilience is among the substantial benefits supplied by plastic shot molding, as the manufacturing process enables exact control over material residential or commercial properties and component style. This accuracy makes sure that the final products show enhanced mechanical strength and resilience, which are essential consider click for more a variety of applications, from durable goods to commercial parts.
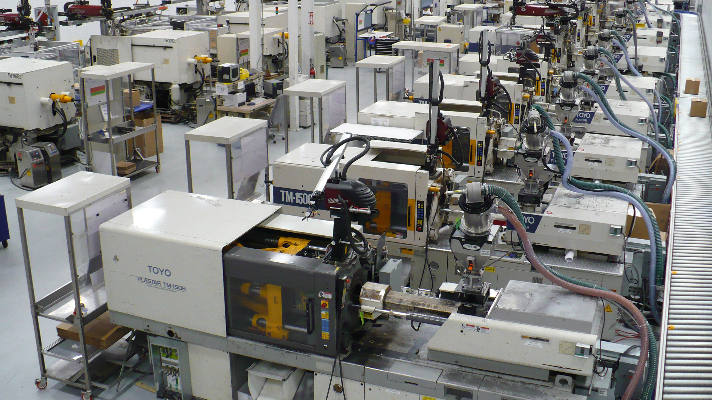
Moreover, the elaborate geometries possible through injection molding enable the production of parts that can endure tension and pressure much better than typical manufacturing methods. The uniform wall surface thickness and lowered material waste additionally contribute to the overall honesty of the product, decreasing the opportunities of failing throughout its lifecycle.
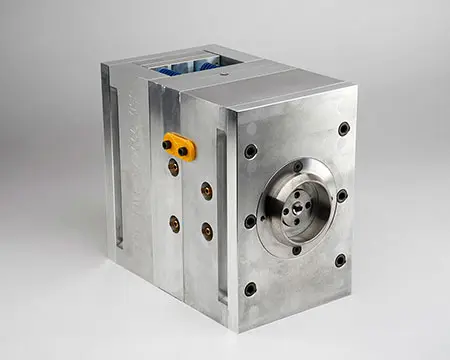
Verdict
In final thought, plastic shot molding presents considerable advantages in manufacturing, consisting of high production effectiveness, style flexibility, and cost-effectiveness. check my blog These variables jointly develop plastic injection molding as an optimal solution for mass production applications, resolving the vibrant demands of modern-day production atmospheres.
Plastic injection molding has actually emerged as a critical method in the production market, using a range of benefits that dramatically boost production processes.One of the most significant advantages of plastic shot molding is its high production effectiveness, which can result in the quick production of thousands of the same components within a brief duration. Plastic Injection Molding.The capacities of plastic injection molding expand past high production efficiency to include considerable layout adaptability.In conclusion, plastic shot molding offers her explanation considerable advantages in production, including high production efficiency, style versatility, and cost-effectiveness. These elements collectively develop plastic injection molding as an optimum service for mass manufacturing applications, resolving the vibrant demands of modern manufacturing settings